Being someone who has researched and studied the aerodynamic devices on an aircraft, I have always wondered about the use of aerodynamic devices from two perspectives. Specifically, I always wondered how the wings can be used for more than just producing lift. This was what sparked my idea of dual-purpose wings, devices that generate lift and help improve the efficiency of aircraft. While this may sound impossible or irrational, I believe this could change the way we look not just at wings, but all aerodynamic surfaces of an aircraft.
The fixed-wing, as I have previously discussed, is a marvellous invention that allows the efficient generation of lift while ensuring safety and comfort. The wing is a piece of innovation that may never be trumped, and I believe that it is not our goal to invent something better than the wing itself, but rather to make use of this invention the best we can. This is the principle behind the dual purpose wing, to use this invention as something more than just a lift-generating device.
The turbofan engine is another engineering marvel, and it is currently the most widely used method of powering an aircraft. The turbofan engine, as I have mentioned previously, works by taking in air at speed, accelerating the air by burning the oxygen using fuel, and propelling out air of higher mass at a higher velocity. The energy generated by an engine is dependent both on the velocity and mass difference of the air as it enters and leaves the engine. Since power is energy per unit time, the power generated is dependent on the mass of the air per unit time that flows through the engine, and this depends on the speed at which the engine can take in and let out the air. Hence, the more air that passes through the engine in a unit time, the higher the power generated by the engine.
To take in more air, engine manufacturers try to make the mouth of the engine as wide as possible. This allows the turbine to take in more air per unit time, thus producing more thrust. However, the higher the diameter, the higher the drag force, and there exists an optimal diameter for the engine. However, this has already been discussed and is not the purpose of this blog. Therefore, to increase the power generated without increasing the fuel usage, the mass of air entering the engine per unit time needs to be increased without increasing the diameter of the engine. This can be done using the dual-purpose wing.
What is the Dual-Purpose Wing:
The dual-purpose wing (DPW) is a wing that is attached to a region above and in front of the engine of the aircraft. For the purpose of explanation, let’s assume that the engine only takes in the air directly in front of it; that is to say, it only takes in the air that lies within a cylinder with a diameter equal to that of the engine and a length ‘x’ which the engine can suck in. This means that the air even millimetrically outside of the cylinder’s diameter cannot be taken in. In this scenario, the DPW is placed at a distance less than ‘x’ in front of the engine and is placed just above the diameter of the cylinder.
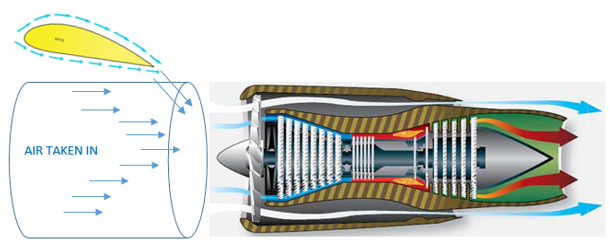
Figure-1: The DPW guiding air into the engine
In Figure-1 above, the yellow body in the DPW. The cylinder represents the region of air that is sucked in by the engine. As the diagram shows, the DPW is placed above the region of air and in front of the engine.
The DPW, like a regular wing, directs air downwards when air is passed over the wing. By this process, the DPW is able to generate lift. However, in serving its purpose as a wing, it indirectly helps the engine by guiding air downward. Without the DPW, the air that passes over the cylindrical space simply glides over the engine, but with the DPW, this air passes into the cylindrical region. By this process, the air that is directed downward enters the engine, providing an extra mass of air per unit time. The DPW allows more air to enter per unit time, and hence the mass of air that enters the engine per unit time is higher.
As previously mentioned, to increase the power generated by the engine, the mass per unit time that enters the engine needs to be higher. This is effectively accomplished by the DPW as it allows for the extra air that is normally wasted to enter the engine, thus producing more power while keeping the fuel usage the same. This not only allows for generation fo aerodynamic lift but also higher effective thrust.
FACTORS TO CONSIDER:
The higher the velocity of air flowing over the wing, the higher the lift generated by the wing. When enough air is passing over the wing and when the engine is running, the engine’s front turbine sucks in air. With the DPW, this includes the downwashed that comes from the DPW, and this hence increases the speed of air that flows over the DPW. when the velocity is higher, the lift generated by the DPW is higher, and the volume of air that is downwashed is higher. As a result of this, the DPW increases lift generated by using the engine while simultaneously increasing the power generated by the engine.
When the engine is at different operating levels, the distance ‘x’ could vary. As a result of this, the DPW may be ineffective at certain distances from the engine. This can be fixed by adding a movable mechanism to the GPW. This way, the position of the GPW can be varied by computer software that changes the GPW’s position relative to the engine’s power output. The DPW can be moved along the x-axis, that is to say, it can be moved to or away from the engine’s front face.
The DPW may be attached to the plane either on the side of the fuselage or through an extension of the wings. This depends on the camber of the DPW as well as the downwash it can produce. The DPW can be kept closer to the engine when the downwash is at a higher angle, while it is kept further away for a lower angle of downwash.
Additionally, the DPW’s width needs to be considered. It only needs to be as wide as the engine itself, and making it any longer could increase drag and reduce efficiency, thus proving to be counter-intuitive.
The DPW’s structural features also need to be considered. The material and the nature of the DPW (hollow/solid/semi-hollow) need to be considered. As the plane travels faster, the force on the DPWs is higher, and hence the DPW’s need to be higher in strength to combat this. Additionally, the DPW’s weight could affect the weight distribution of the aircraft. It could affect the centre of mass and pressure of the plane, causing a huge set of errors. These factors need to be considered to unlock the full capabilities of the DPW’s.
While the DPW’s work well in channelling air to the engines, they could face issues when it comes to interference with the wings. The air that is channelled to the engines (by the DPW) is the air that would, without the DPW, pass over the fixed-wing of the aircraft. When the air that is passed over the wing falls, the lift generated by the wing falls. This could lead to reduced lift, leaving the situation far worse than before. To prevent this disastrous issue, wind tunnels and thorough aerodynamic testing needs to be considered to find the optimal position of the DPW.
All in all, the DPW is just an idea that I had to improve the world of aircraft. While there is a multitude of factors to consider, this is not uncommon in the world of mechanics and aeronautics. I believe when engineering, planned, constructed and implemented, the DPW could be one of the vast ways to improve the efficiency of aircraft today. While DPWs may not be the next big thing, I am extremely happy with the idea that I came up with. I hope to think up such fascinating concepts and bring them to light in this blog!